At DISPENDIX, quality is of utmost importance when it comes to our products. That's why we have implemented rigorous quality control (QC) measures to ensure that every product we deliver meets the highest standards. Through our commitment to quality, we aim to provide our customers with products they can rely on.
By maintaining strict QC practices, we can identify any potential issues early in the manufacturing process and address them before they become larger problems. This helps us to minimize defects and ensure that our products consistently meet the expectations of our customers.
Implementing Rigorous Quality Control Practices
Implementing quality control (QC) measures is a vital part of our manufacturing process at DISPENDIX. It starts with the selection of high-quality materials that meet our strict standards. Our dedicated QC team is responsible for conducting thorough inspections and tests at various stages of the manufacturing process.
Our microfluidic source plates, specifically the wells and their corresponding orifices, are hands down the most difficult part of our consumables that requires extensive testing (Fig. 1). We have a large quantity of consumables that we need to deliver to our customers, so we must ensure they meet certain criteria. There are two main criteria our consumables must meet:
- They must dispense precisely onto our target.
- They must have a certain droplet volume, meaning we must ensure that it does not deviate too much between batches.
Only after these criteria are met can the consumables move on to our assembly process. We use a combination of domain expertise, advanced technology and equipment to ensure accurate and reliable results. This includes conducting visual microscopic inspections and performing functional tests to identify any deviations from the desired specifications. These measures help us to identify and rectify any issues promptly, ensuring that only consumables that meet our rigorous quality standards are delivered to our customers.
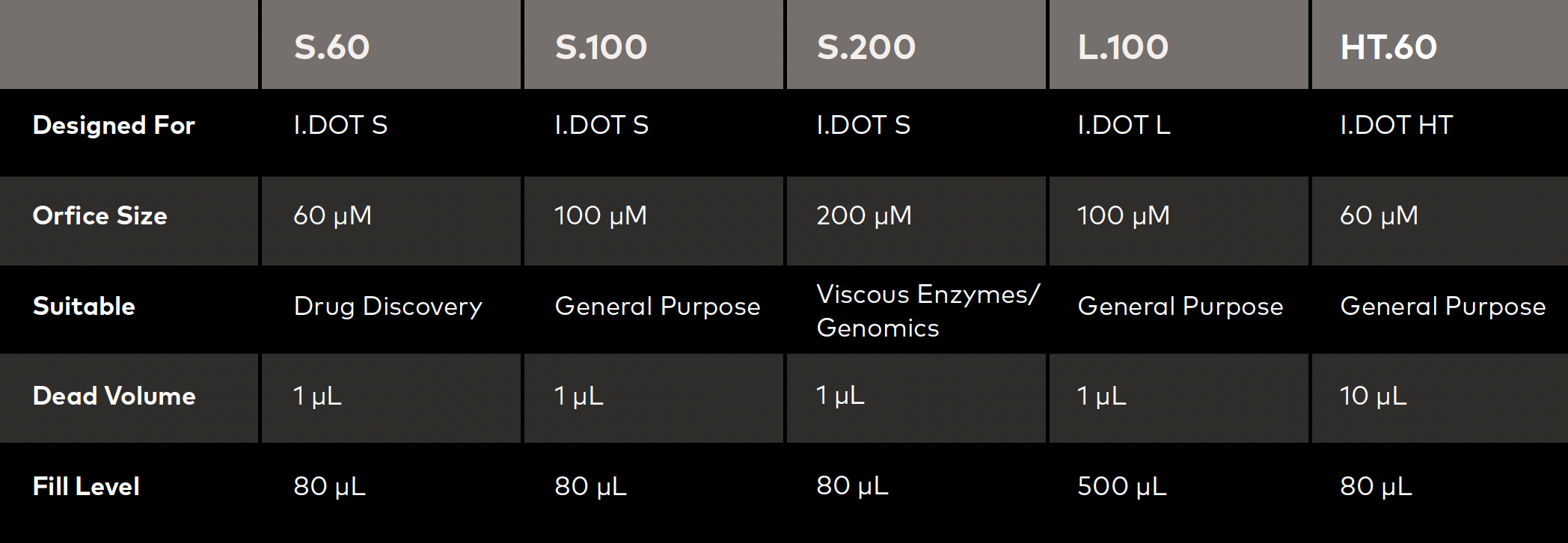
Figure 1. I.DOT source plates are dispensing plates that are compatible with a variety of liquids. The range includes aqueous solutions containing salts and reagents used for qPCR assays, DMSO up to 100%, Matrigel and many other liquids commonly used in labs. The dispensing plates can also handle solvents like methanol and acetonitrile. Additionally, liquids dispensing of living cells is one of the strengths of the I.DOT source plates. These source plates are designed to be used with our I.DOT non-contact dispensing systems.
Benefits of Maintaining High Quality Standards
Maintaining high quality standards brings several benefits to both DISPENDIX and our customers. For DISPENDIX, it helps to build a strong reputation as a reliable and trustworthy lab automation provider. When our customers know that they can rely on our products to consistently meet their needs, it enhances customer satisfaction and loyalty.
For our customers, the benefits are equally significant. By receiving consumables that meet high quality standards, they can have confidence in the reliability and performance of both our products and their data. This helps to minimize downtime, reduce the risk of errors or product failures, and ultimately improve their overall productivity and efficiency in the lab.
Continuous Improvement in Quality Control
At DISPENDIX, we believe in the importance of continuous improvement in QC. We actively seek feedback from our customers and use it to drive improvements in our processes and products. We also encourage a culture of continuous learning and development among our QC team.
By receiving feedback from both our colleagues and our customers, non-conformities, complaints, suggestions, and improvements are reviewed, discussed, and evaluated by the DISPENDIX quality team on a regular basis. This includes investing in R&D to explore new technologies and methodologies that can enhance our QC practices. Because our quality team has a lot of experience in evaluating and doing the quality control of liquid handling devices, we work closely with our R&D team. Our quality team supports them by testing new developing products as well as developing new processes whenever these products have serial production.
By staying updated with the latest industry trends and best practices, we ensure that our team is equipped with the knowledge and skills needed to maintain and improve our quality standards. Through continuous improvement in quality assurance, we strive to exceed the expectations of our customers and deliver products that consistently meet their needs and improve their lives in the lab.